We continue in our filling center, which was officially inaugurated in 2013.
Here some information about the filling process:
1. Unpacker
The empty crates arrive at the unpacker from outside via the conveyor belt. There, the bottles are separated from the crates. At full capacity, our unpacker separates up to 14,000 bottles per hour from the crates.
2. Washing machine
The empty crates are now transported to the crate washer. Transport takes place via the crate turner on the rear side. The empty bottles, in turn, run into the bottle washing machine. A maximum of 12,000 bottles per hour are washed there. The duration of a washing process is approx. 18 - 20 minutes.
3. Inspector
The bottles are then transported to the inspector via a conveyor belt. There they are checked to see whether any impurities or residues are still in the bottle. Unclean bottles are sorted out directly.
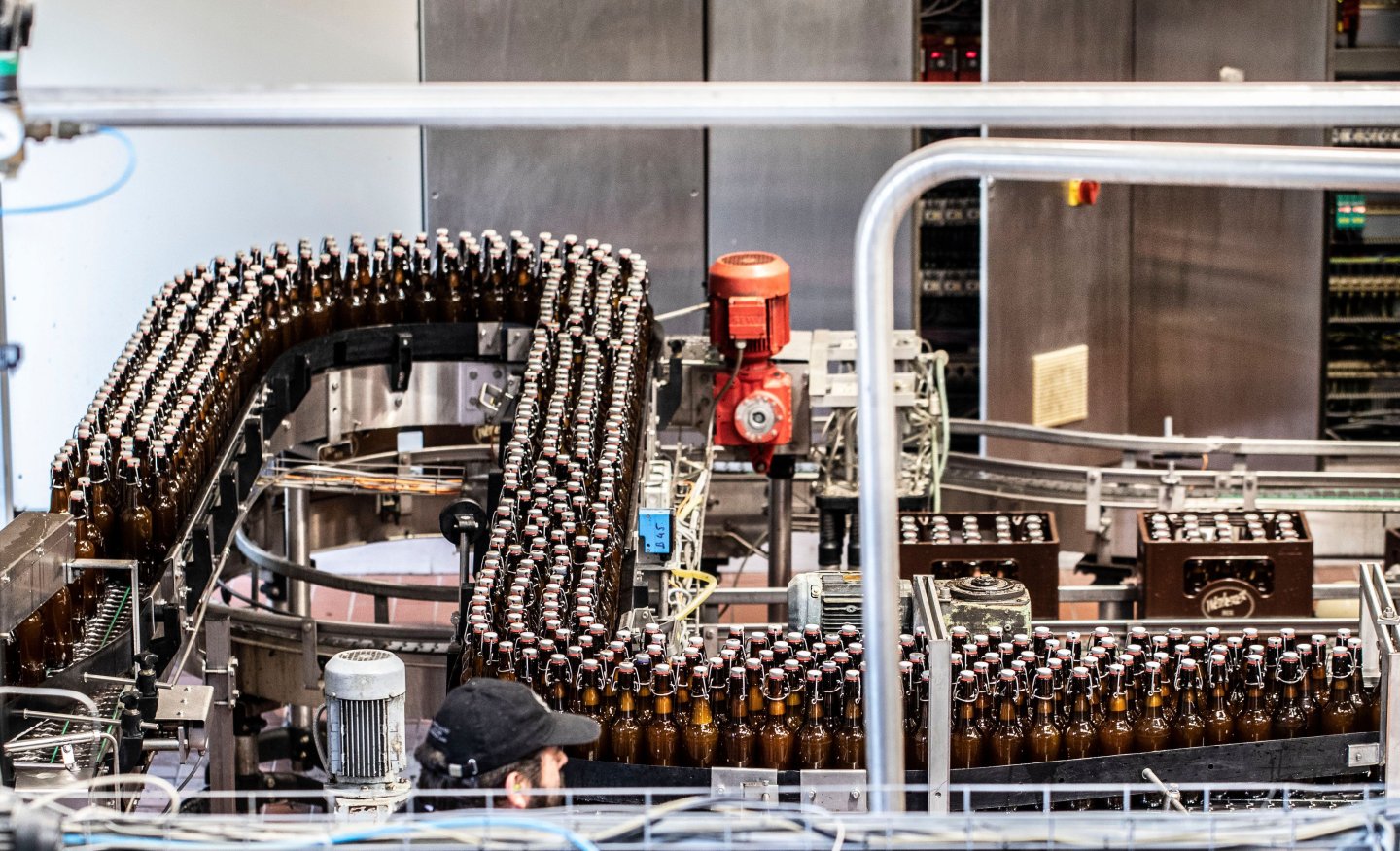
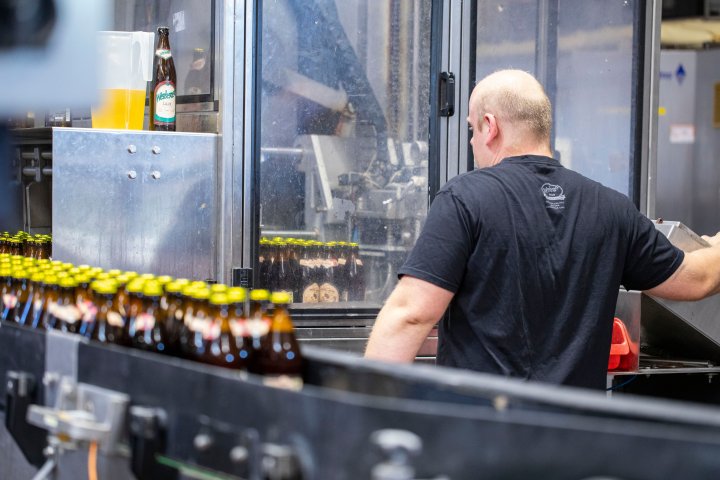
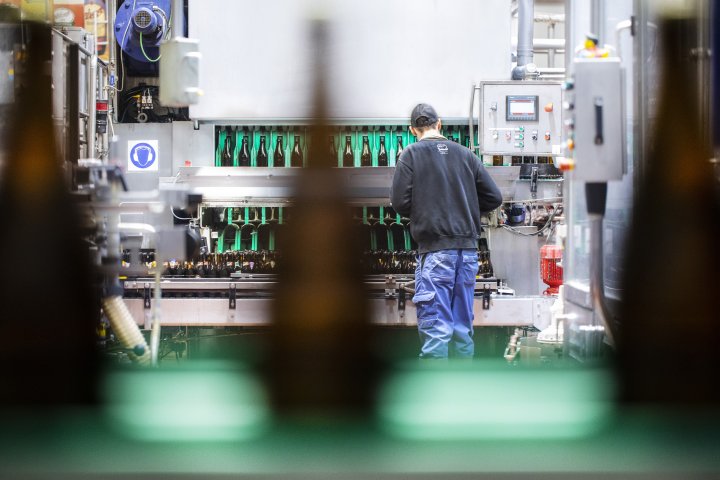
4. Bottle filler
The bottle filler is a fully automatic machine and can fill up to 12,000 bottles per hour.
After the bottles have been filled, they are sealed with crown corks or swing stoppers and subjected to an ultrasonic bath to check for leaks. The bottles are then given their „Weiherer dress“ and given the Weiherer label. In a final inspection, the proper filling is finally checked once again.
5. Packaging
Just as it should, everything comes together again at our packing station. The cleaned crates are filled with the full bottles of our Weiherer beer, return to the logistics hall, and from there start their journey to the customer.
6. Barrel filling
Our KEG filling plant (cleaning and filling plant for barrels) is located in the rear part of the hall.
We fill all common barrel quantities. These are 10, 15, 20, 30 and 50 barrels. Also in the portfolio: the five litre party can.

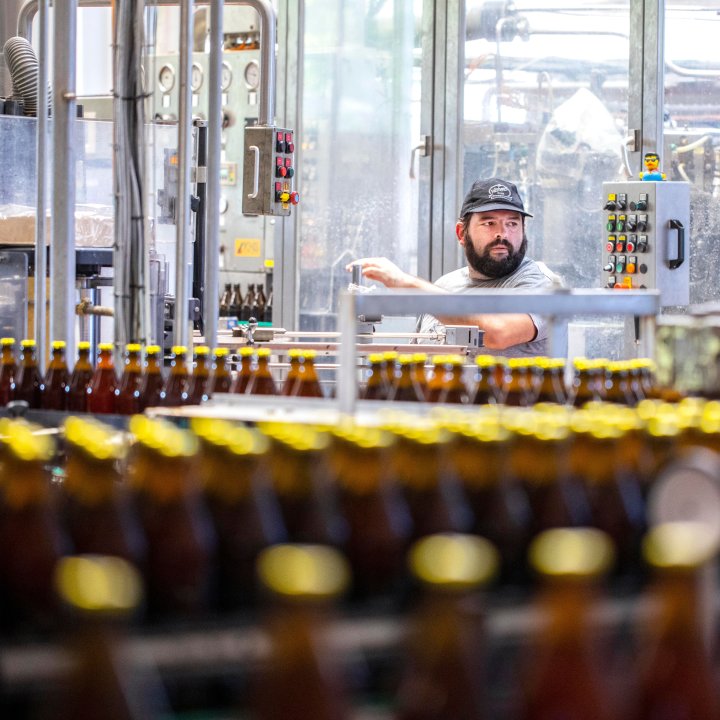
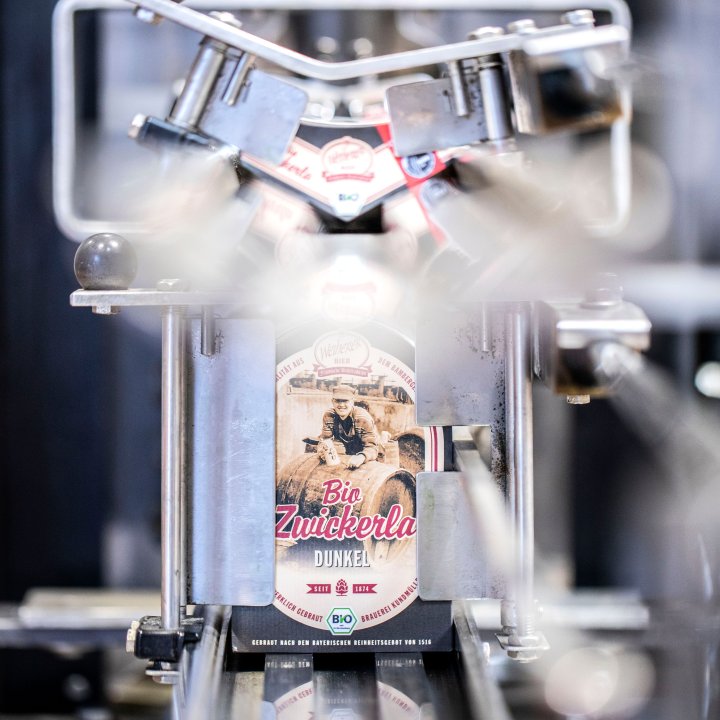